NC Press Brake
video
Watch the video to learn about the product.
Core Components
Our Torsion-sync NC Press Brake features a high-quality torsion bar system that ensures bending precision and long-term stability. Combining an easy-to-use NC system with a robust structure, it meets diverse sheet metal processing needs, excelling particularly in high-precision and repeatable tasks. Equipped with a high-strength steel frame and optimized hydraulic system, it delivers exceptional durability and reliability. Additionally, it offers outstanding cost-effectiveness, providing advanced performance at an affordable price—making it the ideal choice for customers aiming to achieve efficient production while keeping costs under control.
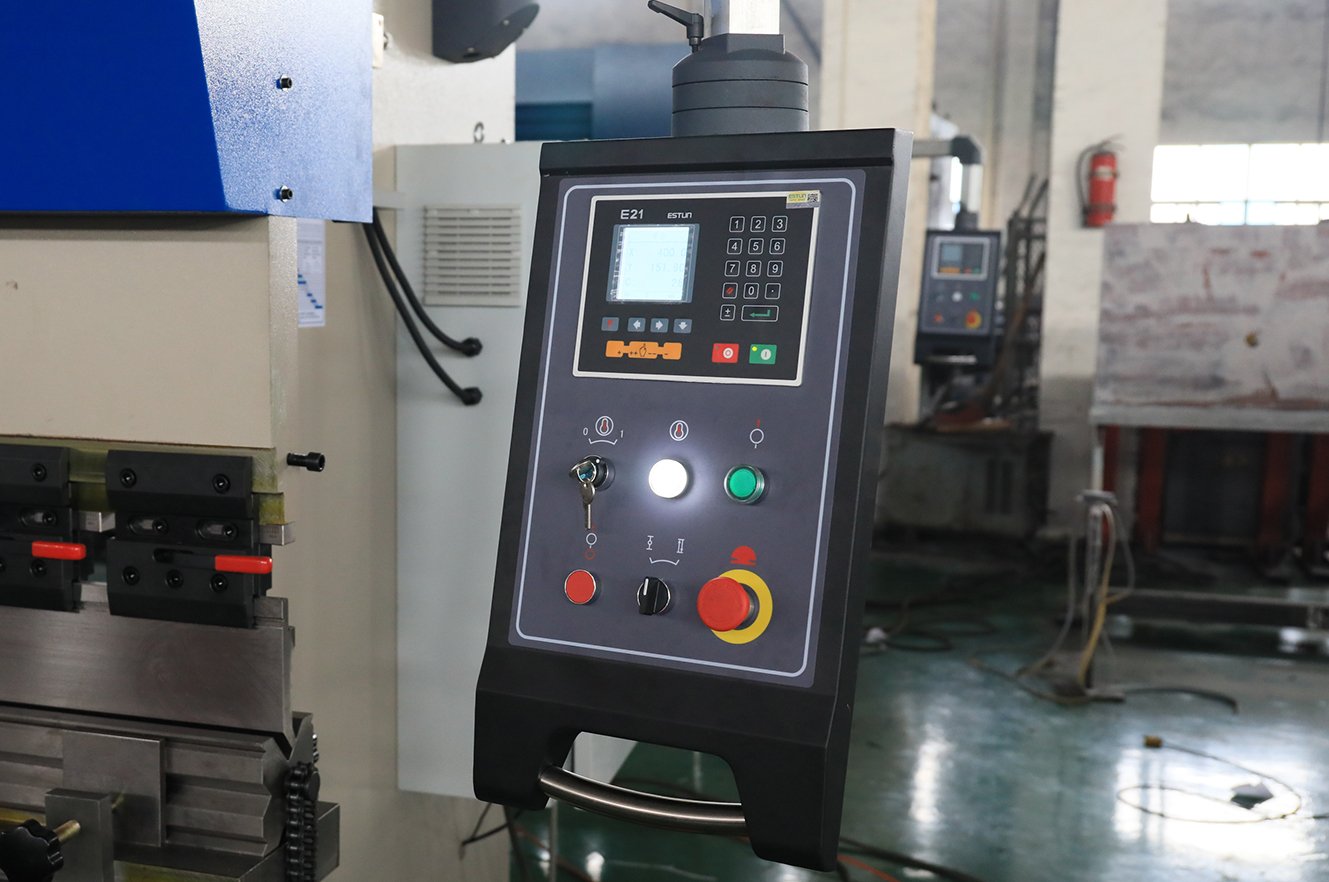
CNC system
- Torsion-sync NC press brakes are often equipped with a variety of CNC systems to meet different processing needs and budgets. Commonly used systems include ESTUN E21 and E300, which are economical and practical and suitable for basic bending needs;
- DELEM DA41T and DA-52S provide more advanced angle control and multi-step programming, suitable for bending tasks of medium complexity;
- Italy’s ESA S530 and S630 systems have graphical programming interfaces and multi-axis control, suitable for high-precision and complex bending;
- Swiss Cybelec DNC 60 is known for its stability and good user interface, and supports precision bending operations.
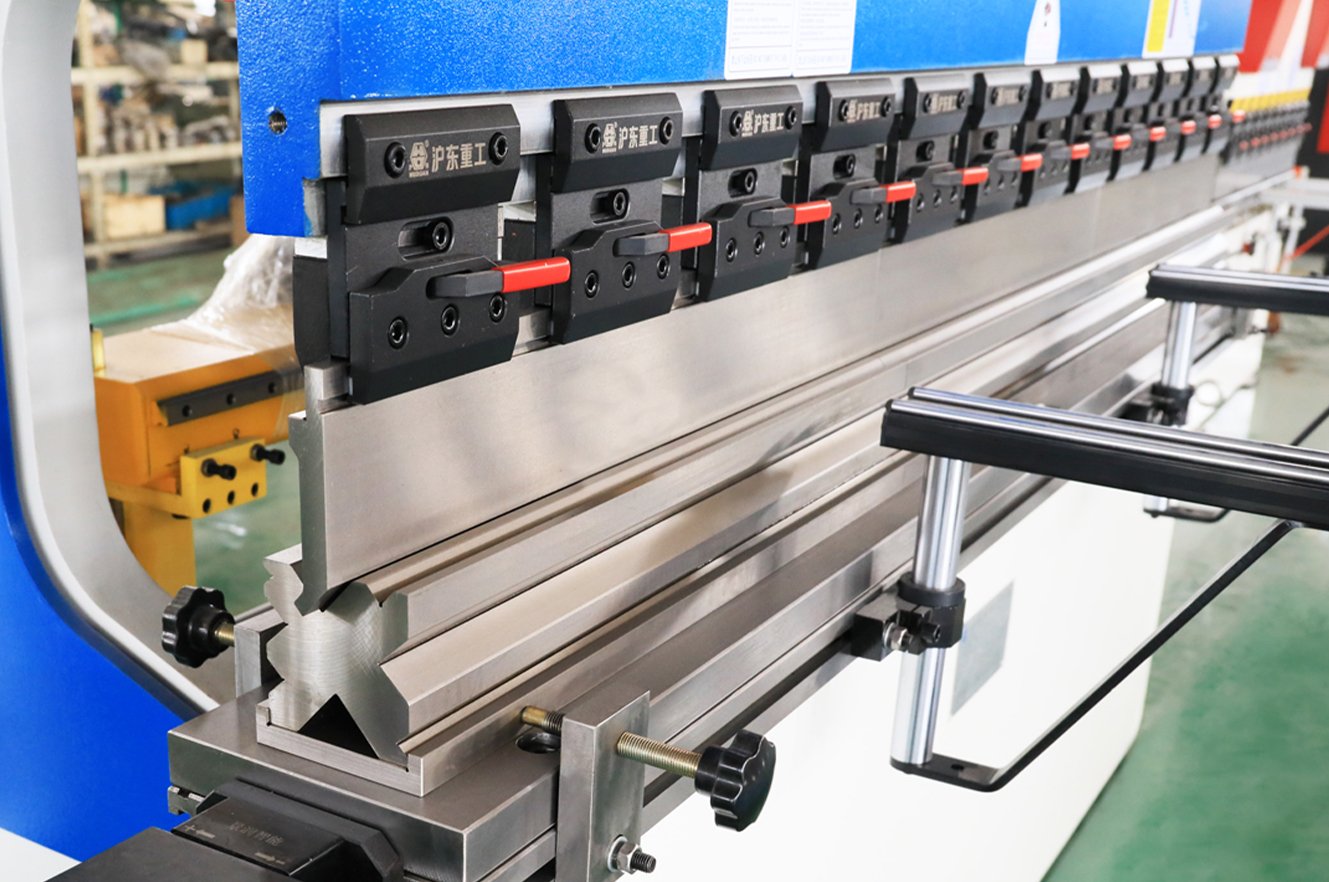
Bending mold
- Toolings are made of 42CrMo mold steel, with an overall hardness of 47 degrees, excellent quality, and durability. The upper mold is installed on the slider and is fixed by a precision fast clamping device;
- Using single V and double V molds can make mold replacement convenient and fast, reduce labor intensity, and improve production efficienc.
- The mold supports customizable standard or non-standard molds.
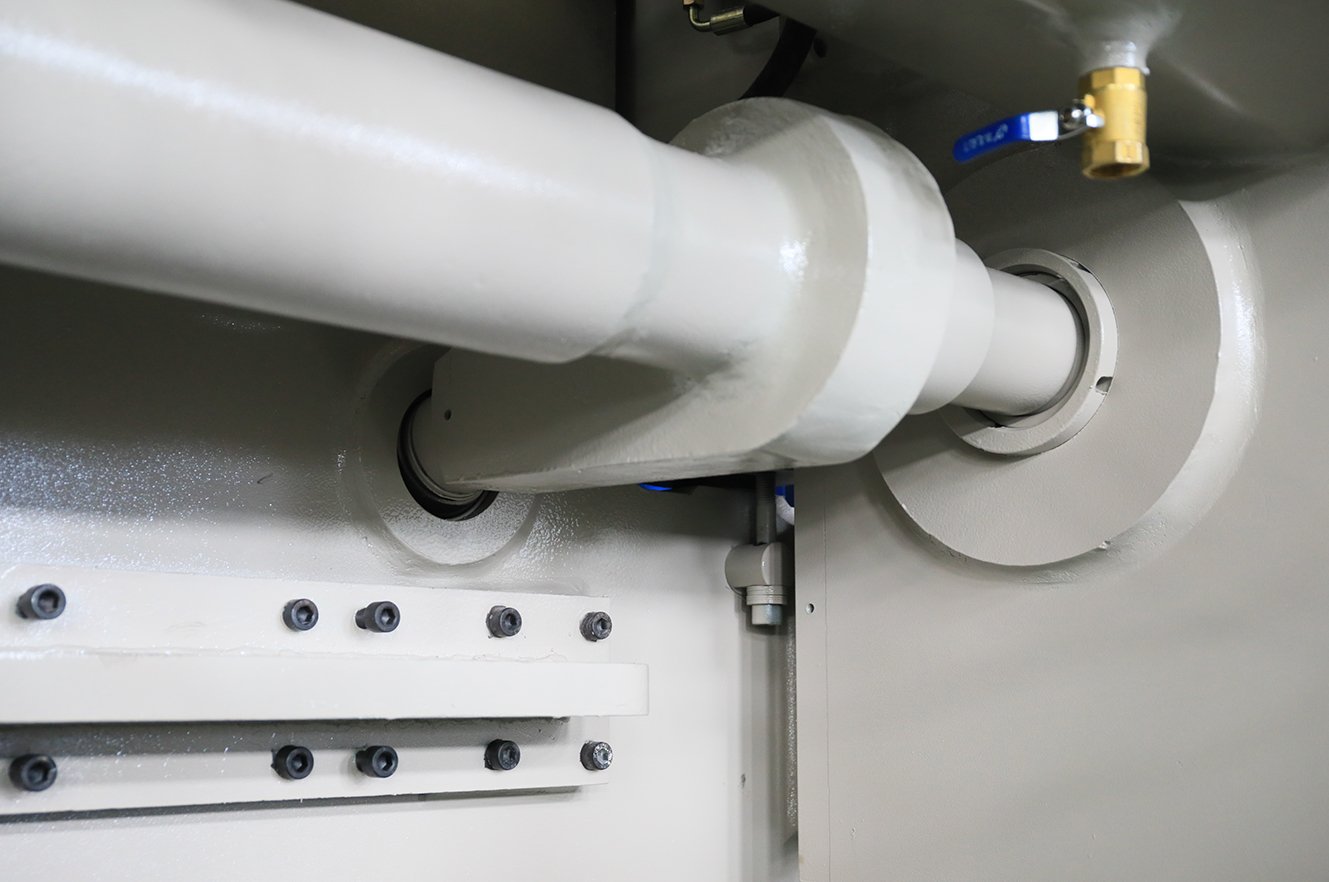
Torsion-sync Bar
- The torsion bar system achieves synchronization at both ends, ensuring synchronization and stability on both sides of the workbench during the bending process.
- This design can maintain high precision under multi-point force application, making the bending angles at both ends consistent, ensuring the flatness and accuracy of the workpiece.
- At the same time, the Torsion-sync Bar has a simple structure, is durable, and has low maintenance costs. It is a core component for efficient and reliable bending operations.
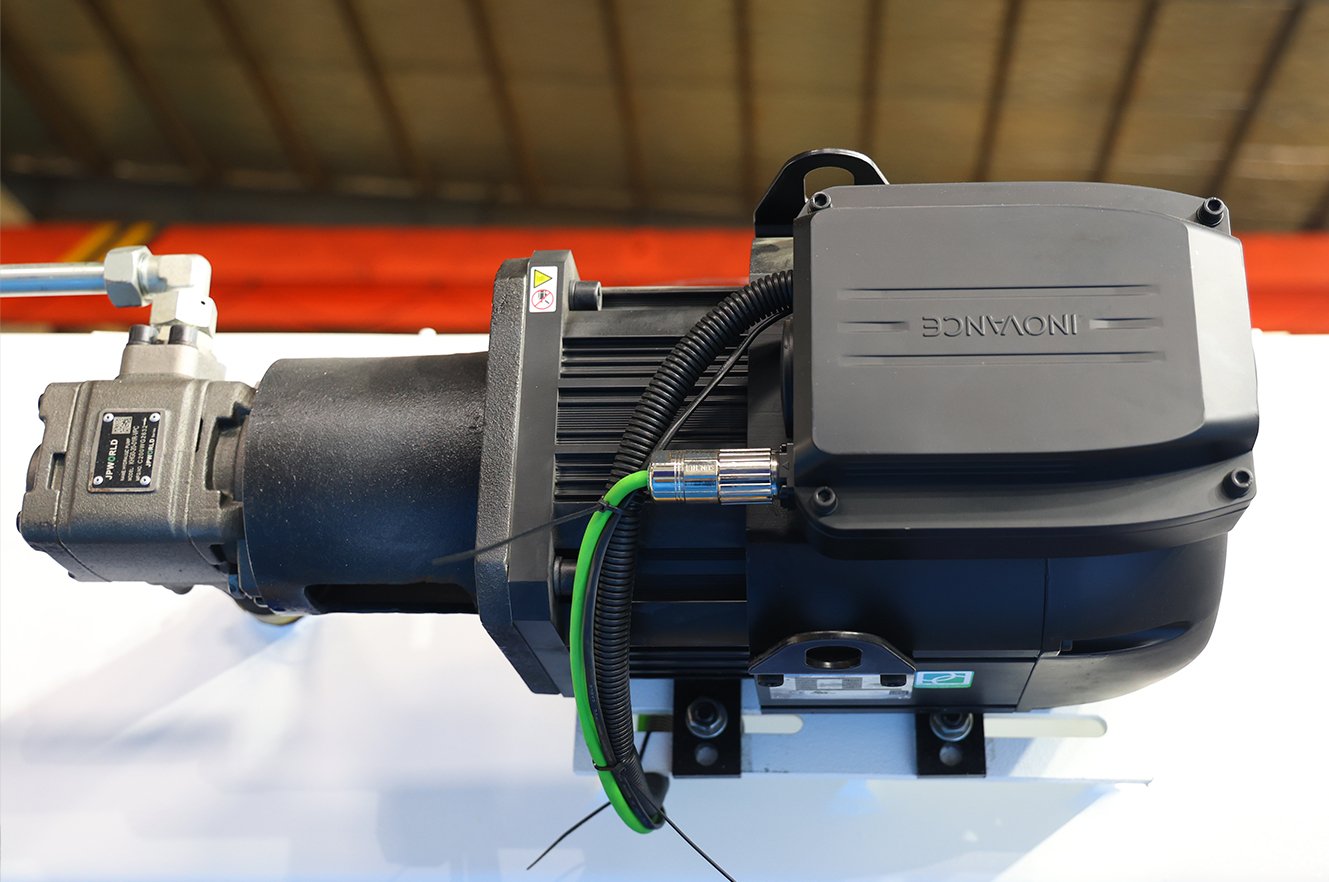
Main motor
- Our bending machines use main motors from world-renowned brands such as Siemens, Bosch Rexroth, and Inovance.
- These motors are known for their high stability, strong torque output, excellent energy efficiency, and precision control. They are not only suitable for long-term load operation, but also ensure the continuous reliability of the equipment under high-precision requirements, helping us provide customers with high-quality and efficient bending solutions.
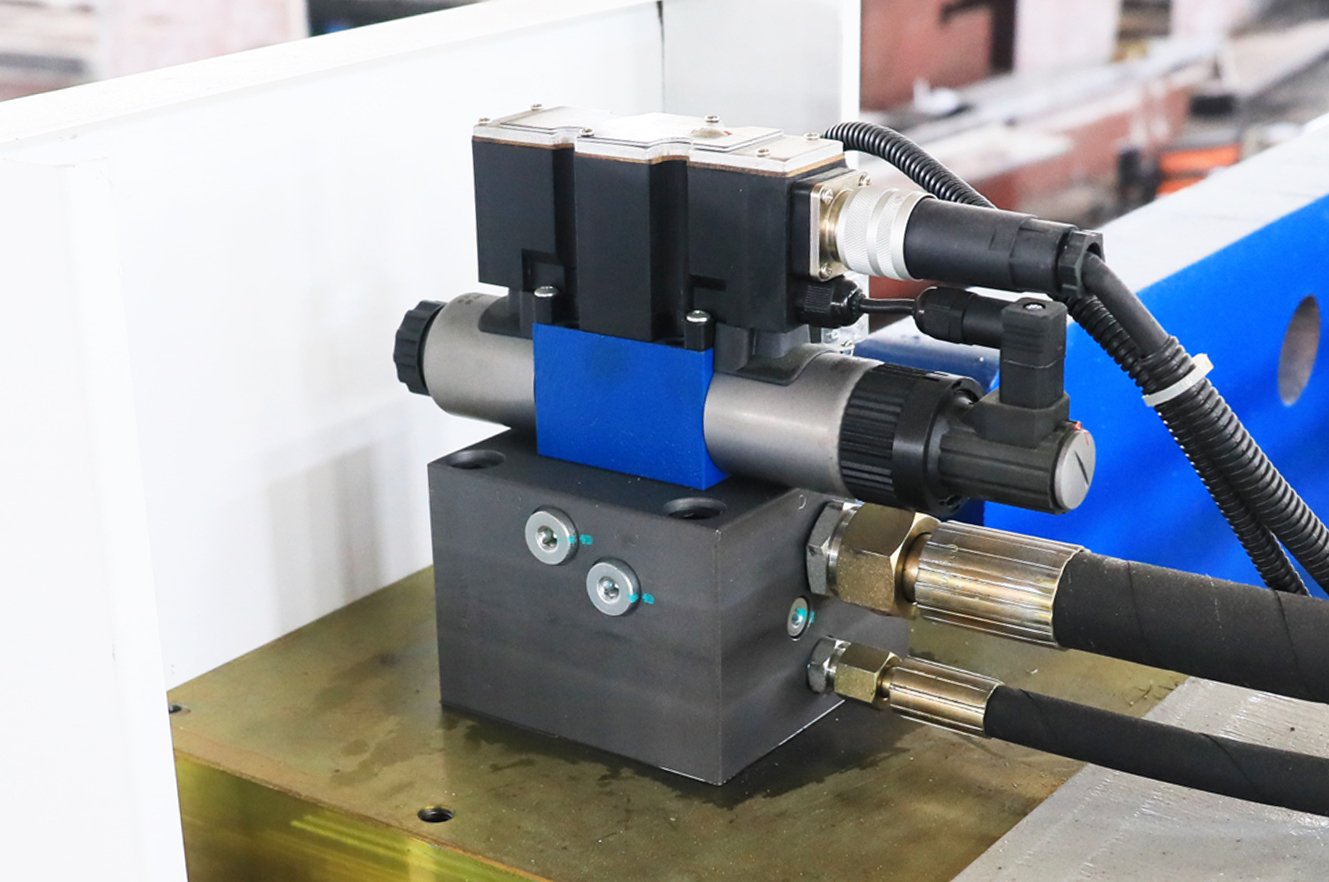
Hydraulic System
- Our hydraulic control system adopts electro-hydraulic servo and synchronous design. The spacing between hydraulic cylinders is very small, with strong anti-eccentric load capacity, high-precision synchronization and excellent power density ratio, and low cost. The pressure of the hydraulic system can be adjusted according to actual needs to meet different bending force requirements.
- For the accessories of the hydraulic system, we chose famous brands such as German hawe and Rexroth, with high efficiency and low failure rate to ensure the reliability of the equipment and the continuity of production.
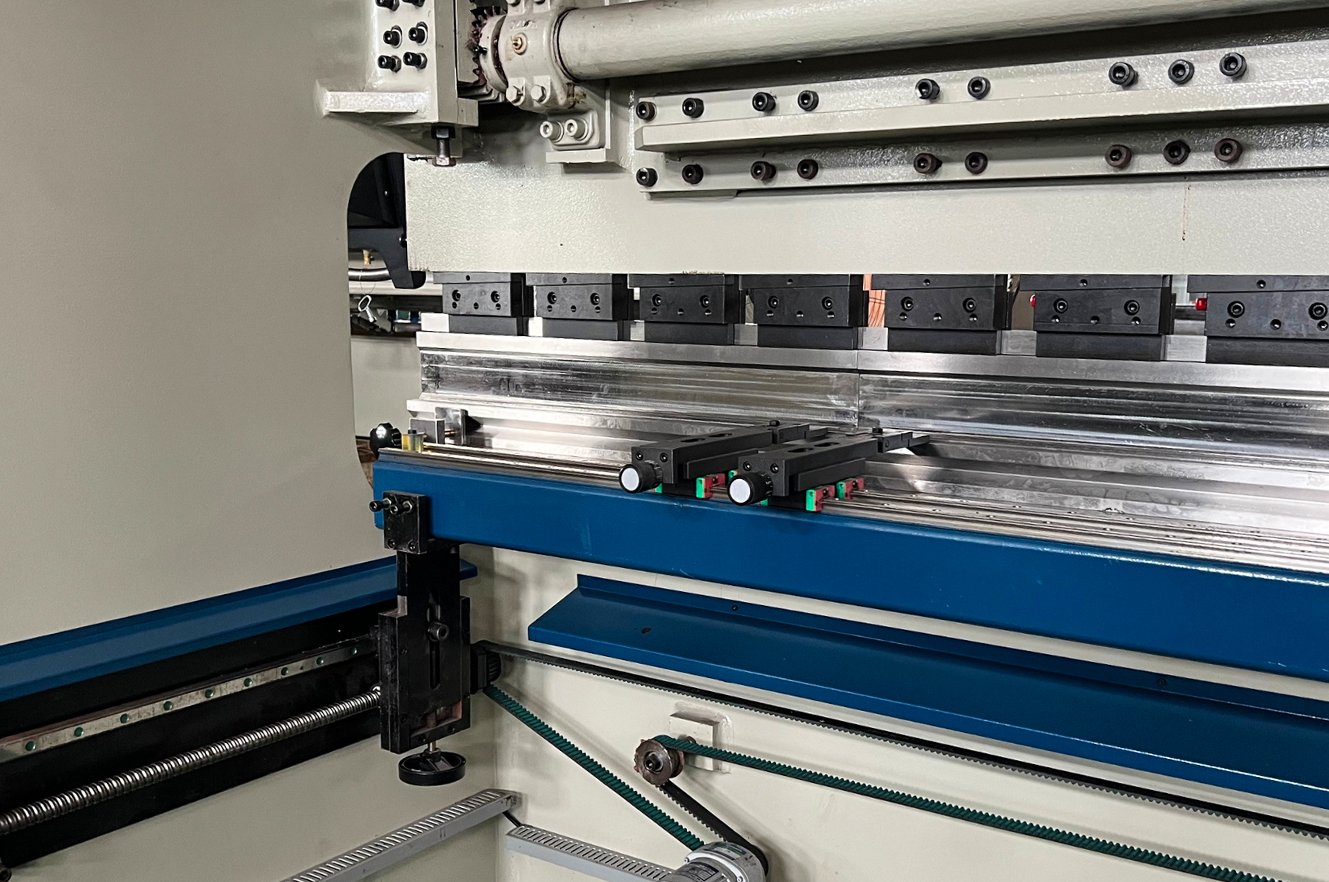
Back gauge device
- The entire back gauge system is subjected to high temperature tempering treatment to eliminate internal stress, enhance the plasticity and toughness of the metal, and avoid loss of precision due to frame deformation
- In order to ensure the motion accuracy of the X-axis, we use imported ball screws and linear guides to replace the traditional screw design, which greatly improves the accuracy and consistency of the processing process.
- The back gauge uses a synchronous pulley mechanism driven by a servo motor to replace the stepper motor, ensuring better control performance and processing accuracy.
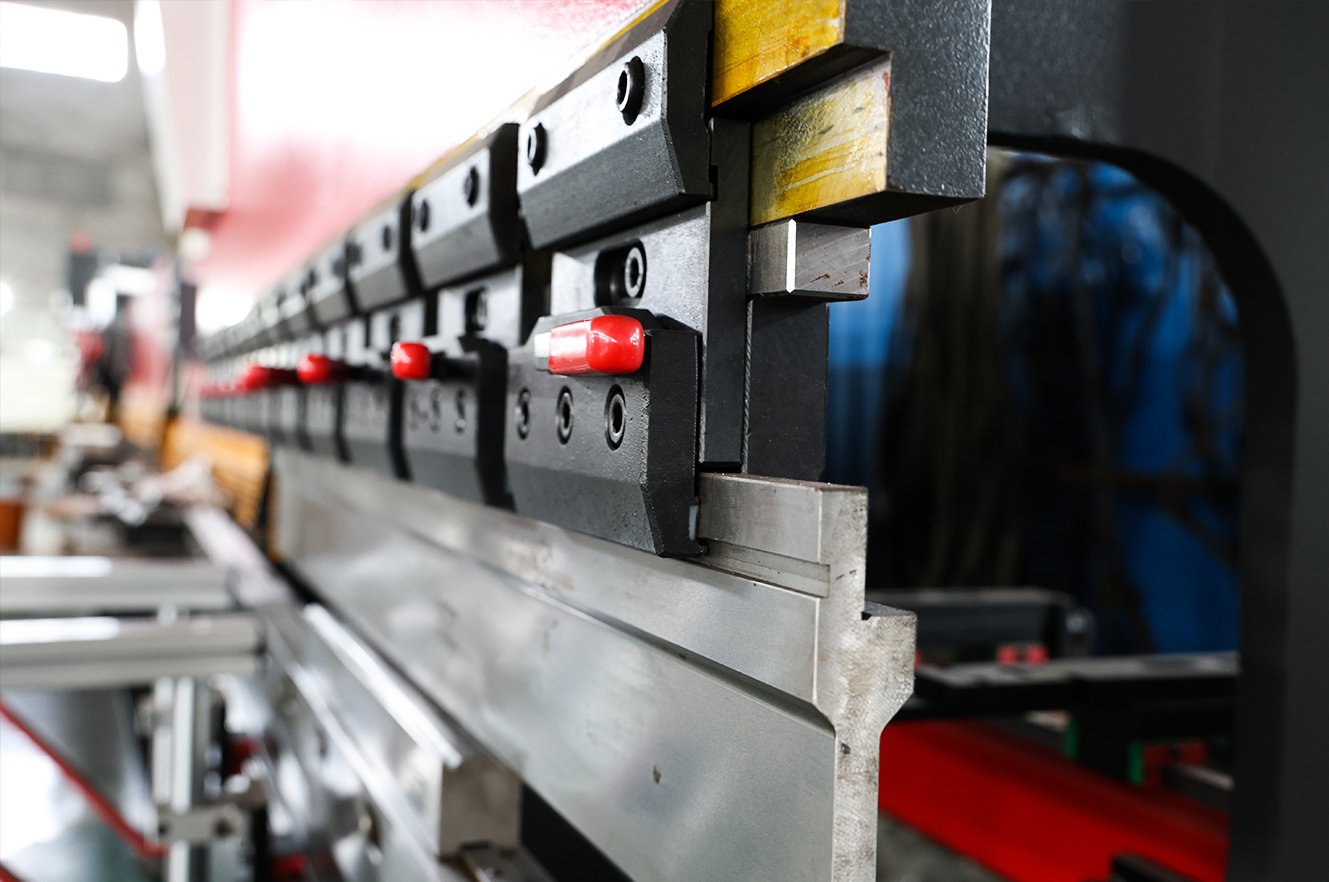
Fast Clamp
- safe and fast tool change
- substantial improvement in timeconsumption and related costs
- Secure against tool falling down
- Available in manual, pneumaticand hydraulic models
- Mounting: Simply from the bottominto the housing, tighten-DONE

Electrical devices
- Our equipment uses high-quality electrical parts that perform reliably even with unstable power supply, and replacement parts are easily available worldwide.
- We use genuine Schneider components imported from France, known for their stability, durability, and long service life.
WF67K Series Technical Parameters:
Type | Nominal force | Worktable length | Poles distance | Throat depth | Stroke | Max open | Power | Dimension |
---|---|---|---|---|---|---|---|---|
(KN) | (mm) | (mm) | (mm) | (mm) | (mm) | (KW) | L×W×H (mm) | |
40T/2500 | 400 | 2500 | 2100 | 245 | 100 | 330 | 5.5 | 2700×1200×1950 |
50T/2500 | 500 | 2500 | 2100 | 245 | 100 | 330 | 5.5 | 2700×1200×1950 |
63T/2500 | 630 | 2500 | 2100 | 300 | 120 | 400 | 5.5 | 2700×1430×2250 |
80T/2500 | 800 | 2500 | 2100 | 300 | 120 | 400 | 7.5 | 2700×1430×2250 |
100T/2500 | 1000 | 2500 | 2100 | 330 | 130 | 410 | 7.5 | 2700×1385×2300 |
100T/3200 | 1000 | 3200 | 2600 | 330 | 130 | 410 | 7.5 | 3400×1385×2300 |
100T/4000 | 1000 | 4000 | 3000 | 330 | 130 | 410 | 7.5 | 4200×1385×2450 |
125T/2500 | 1250 | 2500 | 2100 | 330 | 130 | 410 | 11 | 2700×1385×2300 |
125T/3200 | 1250 | 3200 | 2600 | 330 | 130 | 410 | 11 | 3400×1385×2300 |
125T/4000 | 1250 | 4000 | 3000 | 330 | 130 | 410 | 11 | 4200×1385×2450 |
160T/2500 | 1600 | 2500 | 2100 | 350 | 150 | 450 | 11 | 2700×1590×2480 |
160T/3200 | 1600 | 3200 | 2600 | 350 | 150 | 450 | 11 | 3400×1590×2480 |
160T/4000 | 1600 | 4000 | 3000 | 350 | 150 | 450 | 11 | 4200×1590×2500 |
160T/6000 | 1600 | 6000 | 4600 | 400 | 150 | 450 | 11 | 6200×1620×3000 |
200T/2500 | 2000 | 2500 | 2100 | 350 | 150 | 450 | 15 | 2700×1590×2480 |
200T/3200 | 2000 | 3200 | 2600 | 350 | 150 | 450 | 15 | 3400×1590×2480 |
200T/4000 | 2000 | 4000 | 3000 | 350 | 150 | 450 | 15 | 4200×1590×2500 |
200T/6000 | 2000 | 6000 | 4600 | 400 | 150 | 450 | 15 | 6200×1620×3000 |
250T/3200 | 2500 | 3200 | 2600 | 350 | 190 | 500 | 18.5 | 3400×1690×2480 |
250T/4000 | 2500 | 4000 | 3000 | 350 | 190 | 500 | 18.5 | 4200×1690×2500 |
250T/6000 | 2500 | 6000 | 4600 | 400 | 190 | 500 | 18.5 | 6200×1800×3200 |
300T/3200 | 3000 | 3200 | 2500 | 350 | 190 | 500 | 18.5 | 3400×1785×2870 |
300T/4000 | 3000 | 4000 | 3000 | 350 | 190 | 500 | 18.5 | 4200×1785×2870 |
300T/6000 | 3000 | 6000 | 4600 | 400 | 190 | 500 | 18.5 | 6200×2100×3400 |