Service
Service & Support
We provide comprehensive technical support for the entire product, covering every stage of the product life cycle. From pre-sales consultation, equipment installation, technical training to after-sales support, our technical experts are always at your service.
Help you choose the best equipment for your application.
Choosing the right equipment is crucial before making a purchase. Our experienced technical team and sales consultants work closely with you to understand your production process, product specifications, and factory layout. Through detailed communication and needs analysis, we can recommend the most suitable equipment models and technical parameters to maximize production efficiency and cost-effectiveness. We also offer on-site inspection services to help evaluate production needs comprehensively, ensuring that the equipment selection is perfectly aligned with your actual production scenario, avoiding issues such as incorrect selection or inadequate configuration.
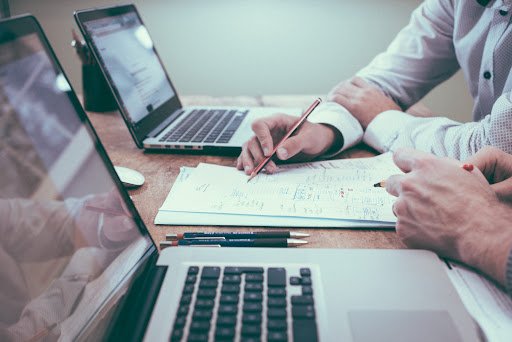
Understanding Your Needs and Tailoring Machines to Fit Your Production Requirements
We understand that each industry and customer has unique requirements, and standard equipment may not suit everyone. To meet these diverse needs, we provide customized equipment solutions. We work closely with you to understand your production process, material characteristics, and factory conditions, then design equipment tailored to your specific requirements. Our R&D and engineering teams maintain close communication with you throughout the process—from design to manufacturing to final acceptance—ensuring that each customized machine meets your exact production goals. This approach allows you to receive equipment fully aligned with your needs, maximizing efficiency and product quality in your production lines.
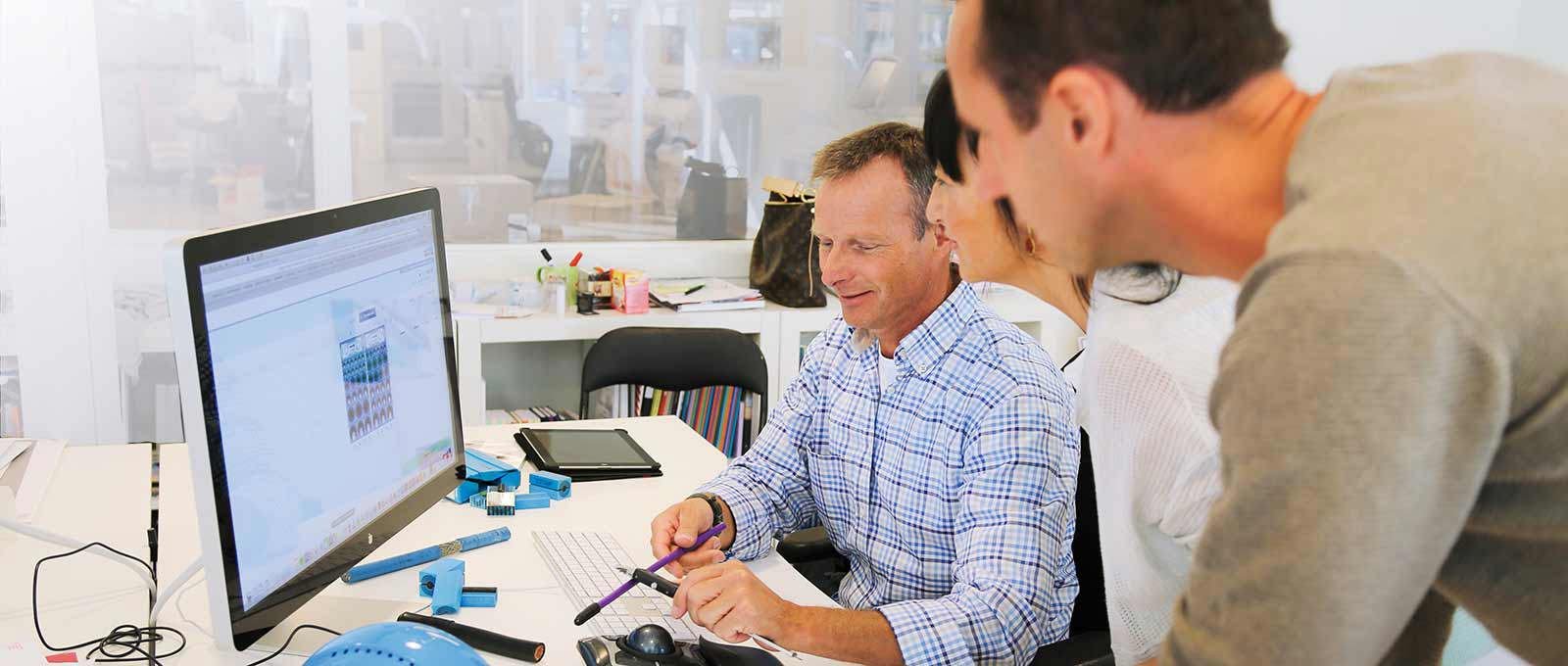
Providing On-Site or Remote Installation Guidance to Ensure Proper Configuration and Commissioning
Once the equipment is delivered, proper installation and commissioning are critical to ensuring smooth operation. We offer comprehensive installation support, whether through on-site engineers for direct installation or remote guidance, ensuring that the equipment is correctly set up in your factory. Our installation team is highly experienced and can quickly identify and resolve any issues that may arise during the installation process. Additionally, we adjust the equipment based on the layout of your production line to ensure it operates optimally, minimizing downtime and errors during the initial run.
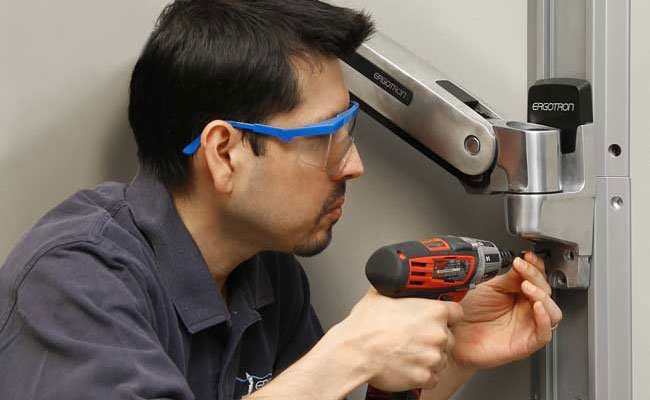
Providing Training for Operators and Maintenance Teams to Ensure Optimal Equipment Performance
The correct operation and maintenance of equipment directly affect its long-term stability and production efficiency. After the installation, we offer systematic training courses for your operators and maintenance personnel. The training covers basic operation, safety protocols, troubleshooting, and daily maintenance. This ensures your team is fully equipped to operate the machines efficiently and perform necessary maintenance, reducing the risk of human error, extending the equipment’s lifespan, and enhancing production efficiency and product quality.
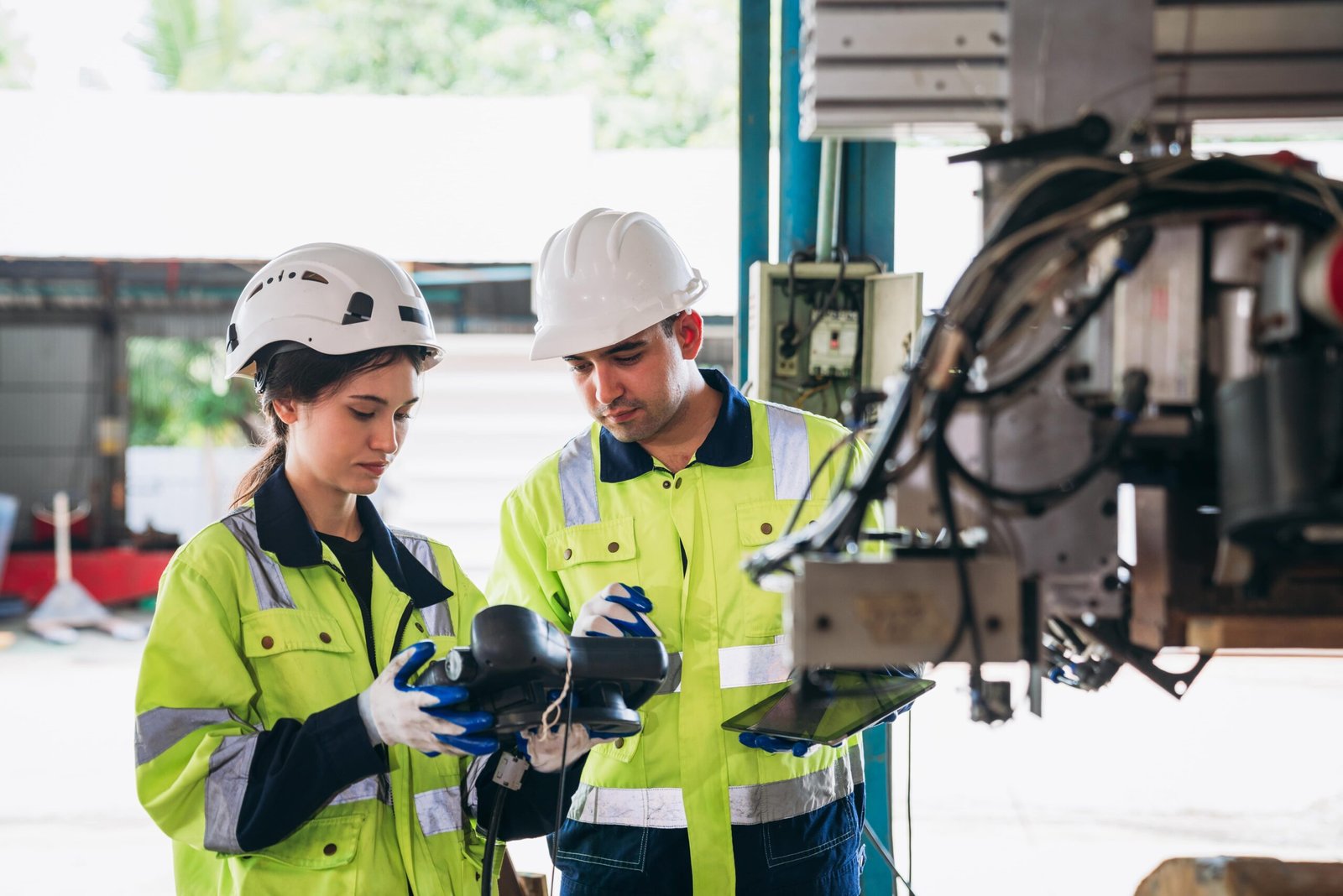
After-sales service
At Hudong Heavy our commitment to customers doesn’t end with the delivery of the equipment. We provide comprehensive after-sales service and maintenance support to ensure your machines continue to operate at peak efficiency throughout their lifecycle. Here’s how we support our customers post-sale
Service Method
Telephone Hotline Service
365 days a year, 7×24 hours per week and company telephone hotline (+86-25-56200956) service support, users can directly contact the company’s technical engineers by phone, ask questions and discuss about products defect and ask for any help, our technicians will give answer in time.
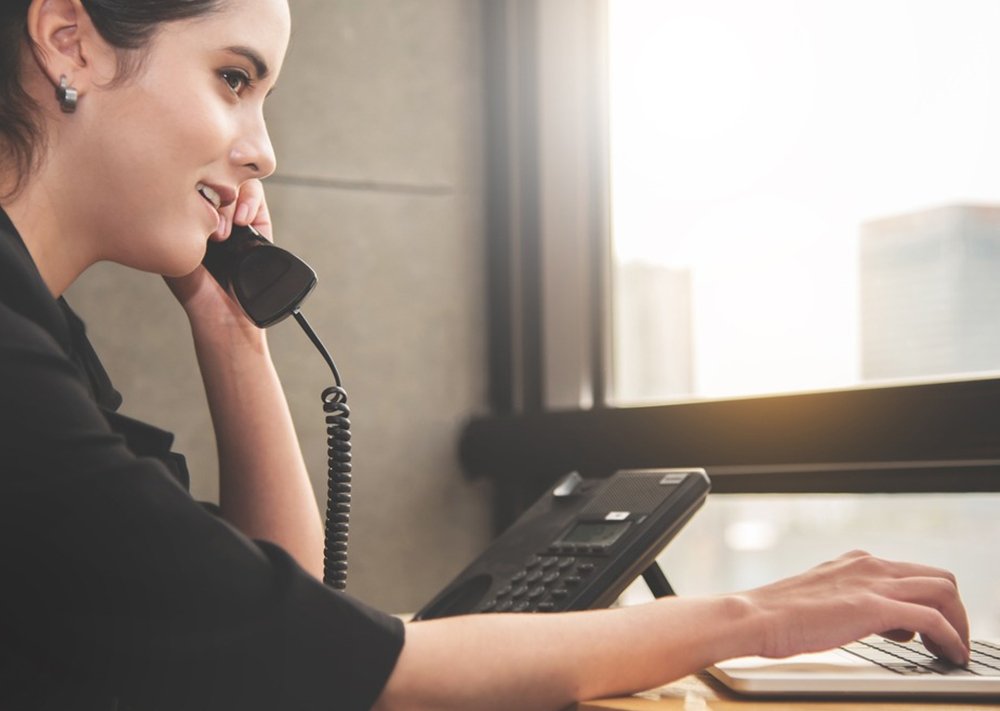
E-mail support service
E-mail service support is available 24 hours per day, 365 days per year.
E-mail: web@ahhudong.com
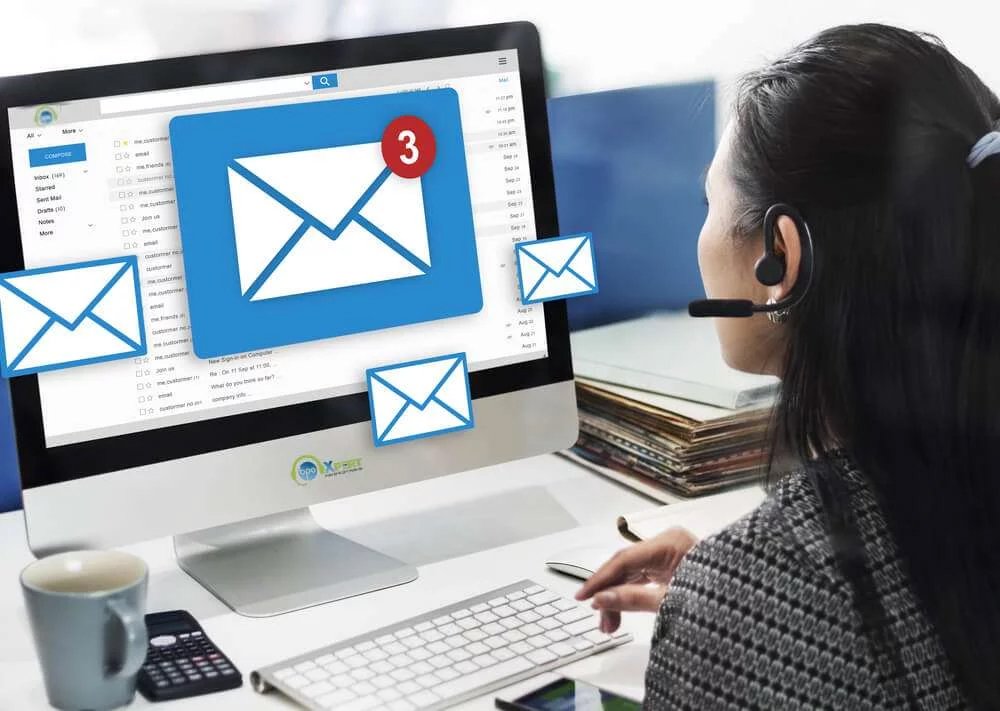
Remote technical support service
The company established a technical support and response center, set up a dedicated person to carry out 7×24 hours on duty, the company can provide users with remote online fault diagnosis, analysis and resolution in time when the user requires.
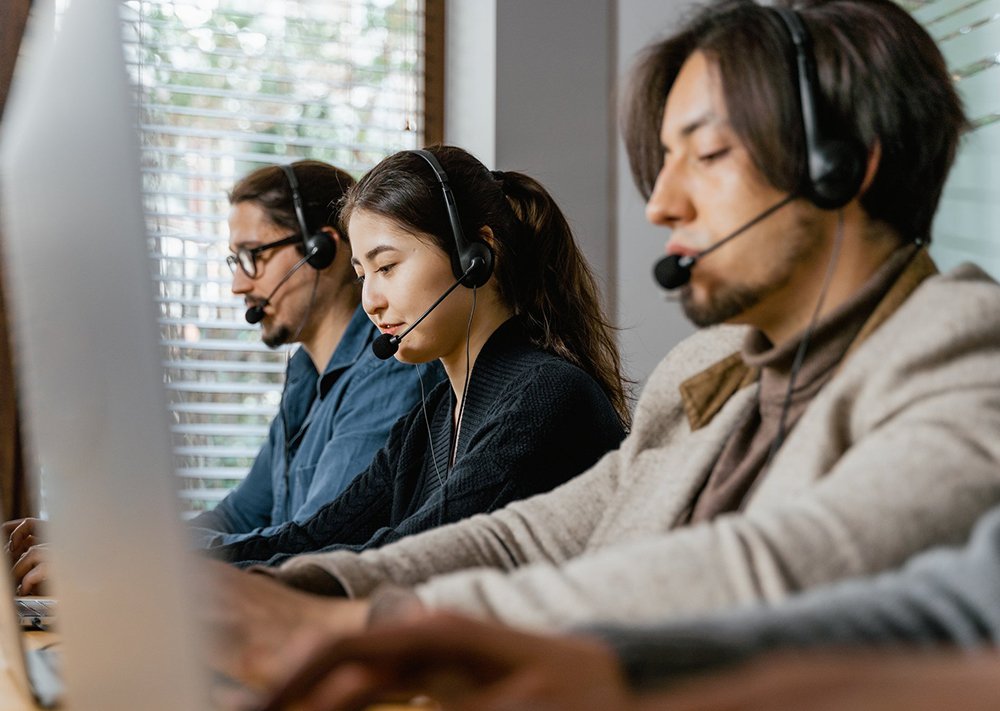
On-site support service
When necessary, the company will send experienced technical engineers to the site to provide services to users. The company’s technical engineers will be in the user’s environment, experience the system’s operating conditions in detail, communicate face-to-face with users, and conduct reliable and effective fault prediction, problem tracking, abnormal troubleshooting, and system optimization.
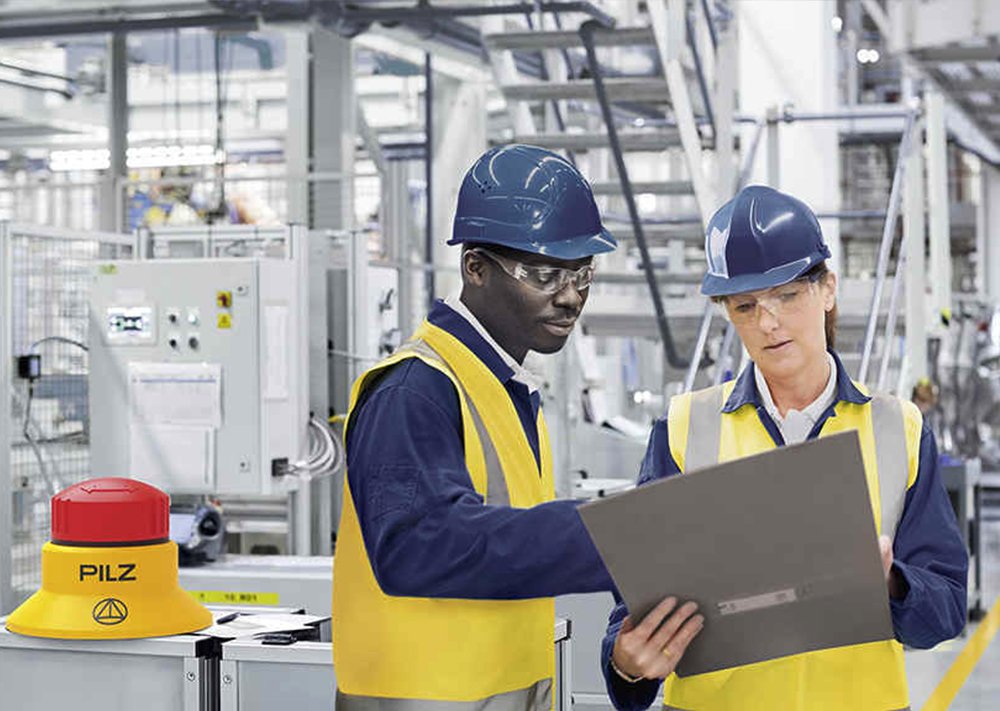